ID Casting, helping your development
Need a specific part? At ID Casting, a multidisciplinary team will help you to
co-design and optimise your products, before designing and manufacturing tooling, industrialising products and optimising the value chain.
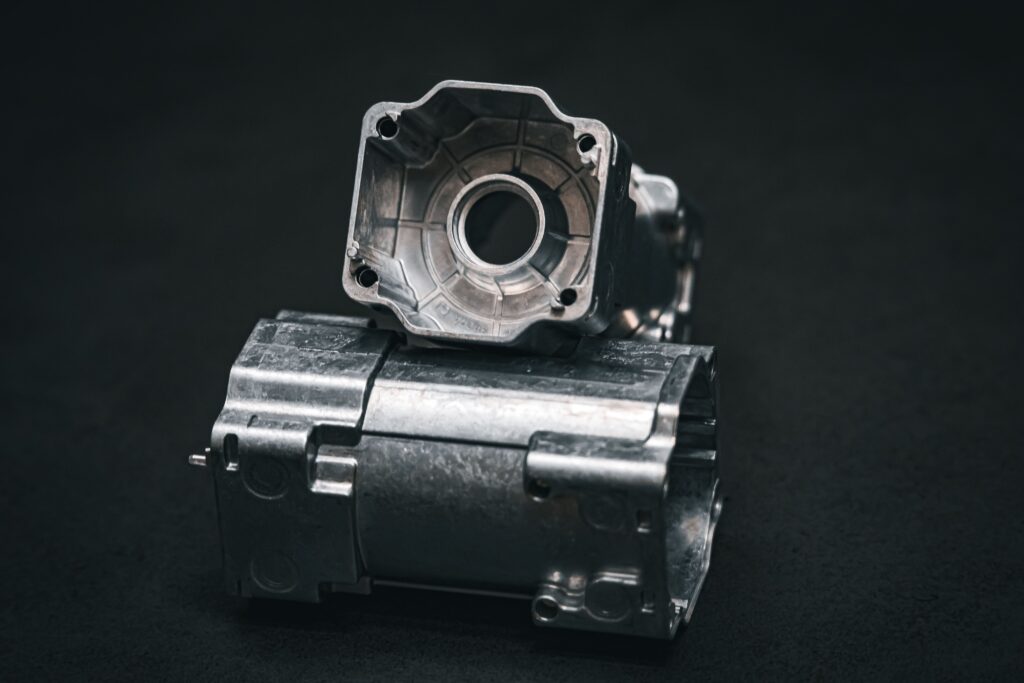
Our mission:
Industrialising customer needs
ID Casting owes its expertise to the wide range of skills that make up the group: a high-level design office that can carry out around a hundred projects a year, a design and production team of around ten people and a stock of 7,000 tools. In concrete terms, what is the life cycle of your project at ID Casting ?
When you call on ID Casting, you are guaranteed a co-design between you and our design office to create a feasible and optimised part: We advise you and work alongside you to meet the needs and uses for the application of your parts. We price up the part and the investment required to make it, as each mould is unique.
A design office
by your side
Then our design office takes charge of designing and drawing all the tooling needed to make your part. Our Creo 8 and Altair Inspire software can be used to create 3D design representations, and to simulate the filling and thermal properties of the part in the mould.
Our ambition? Quality and rigour for a flawless part!
Once this stage has been completed, we start manufacturing the tools in our workshops, or with our partners in France or China. Once delivered, we then carry out the first tests to obtain the first parts, the starting point for all the stages of industrialisation.
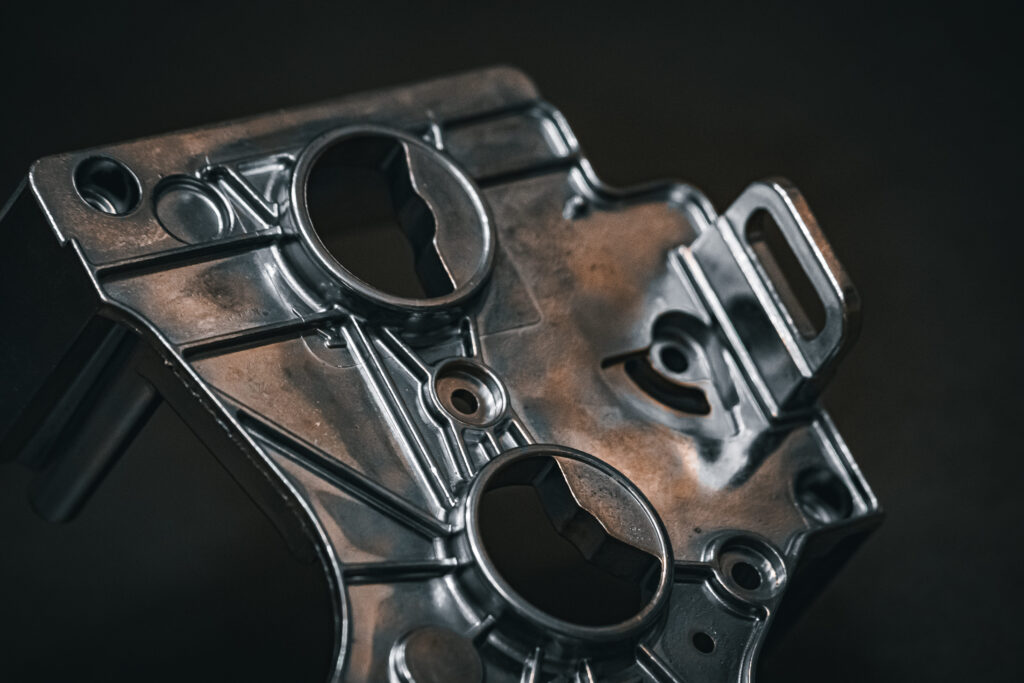
Research and
development
ID Casting is a skilled research and development centre that manages every stage of the process in order to
to provide total satisfaction to our customers and guarantee the quality of the products delivered.
Our motto? Rigour, reliability and performance.
Co-design
optimisation
Prototyping
Tool design
Production and maintenance of tooling
Industrialisation
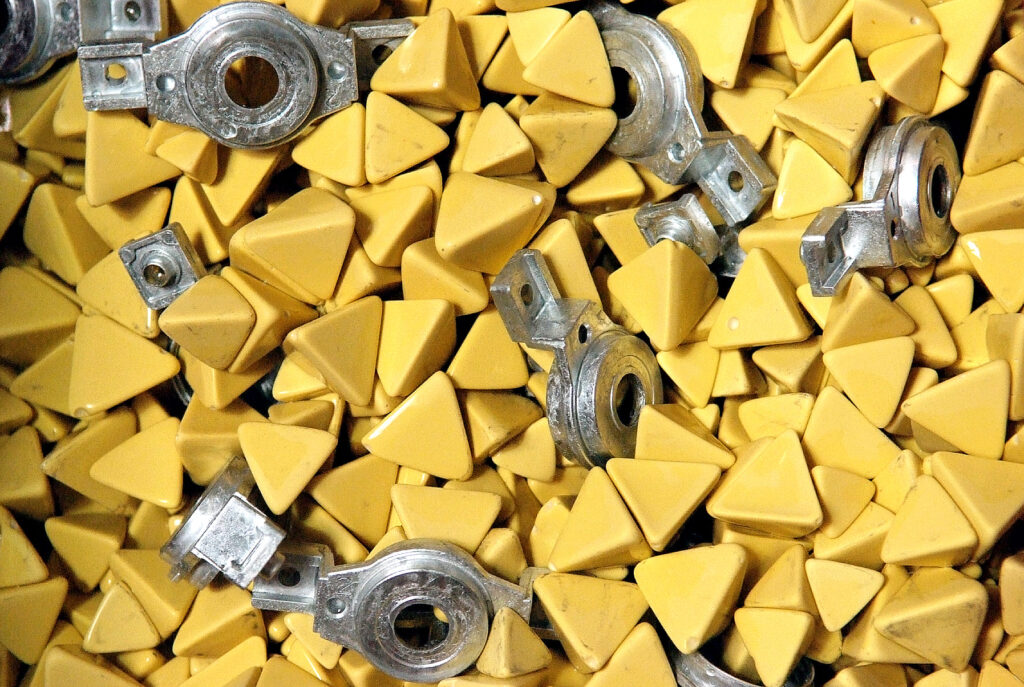
Codesign / optimisation
Our co-design approach with customers enables us to improve both the design and functionality of their products. By taking the entire production process into account, ID Casting carries out analyses and simulations to optimise product and process performance, while reducing costs. This is ID Casting’s strength: Thanks to this close collaboration, we achieve top-quality results that meet the specific needs of each customer.
Prototyping
Do you need a plastic or metal prototype part quickly to carry out mechanical, aesthetic or assembly tests? We can rise to your expectations. ID Casting is equipped with a state-of-the-art 3D printer to produce your plastic prototypes. We also call on our partners to create metal prototypes using vacuum-formed wax-pearls or machined from a unibody. Depending on your requirements and quantities, we are committed to offering you the most suitable material and process, within very short lead times. Our trump card? Reactivity.
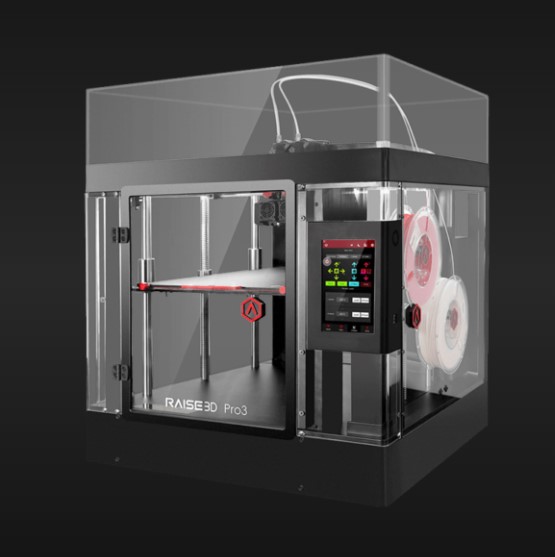
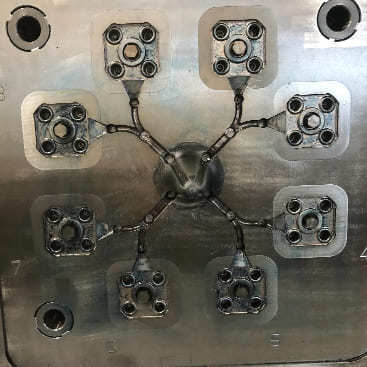
Tooling
design
Our experience and expertise in zinc and magnesium alloy die casting, coupled with the use of the latest simulation and design software, enable our experts to support our customers in the design of their products based on their drawings, specifications and requirements. It is in Arbois, at the Group’s headquarters, that our teams design all the tools needed for the manufacturing process to meet our customers’ requirements.
Our robust, high quality and technically advanced tooling offers you the highest performance and guarantees that your quality objectives and requirements are met throughout the life of your products. Our aim? To provide moulds with exceptional performance by applying best practice, resulting from serious technological monitoring.
Production and maintenance of tooling
Our expertise and know-how in toolmaking are the fruit of solid experience in the field. ID Casting is committed to providing quality, reliable and cost-effective solutions that meet the specific needs of each project.
Rely on our team of experts to make your tools, and benefit from the highest guarantees for your tools.
Your tools are in good hands, monitored and maintained throughout their warranty period.
Our trump card? Each site in the ID Casting group has its own in-house resources for mould maintenance and repair, a guarantee of reactivity! Our strength lies in the methodologies we use to monitor preventive and corrective maintenance, both on products and processes.
Anticipating, optimising and adapting are all part of the ID Casting group’s ethos.
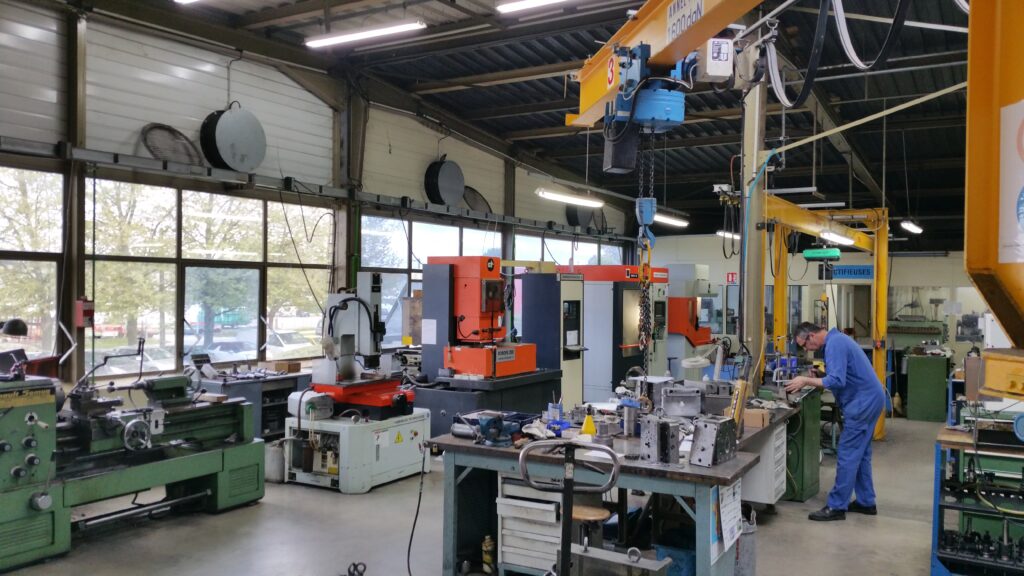
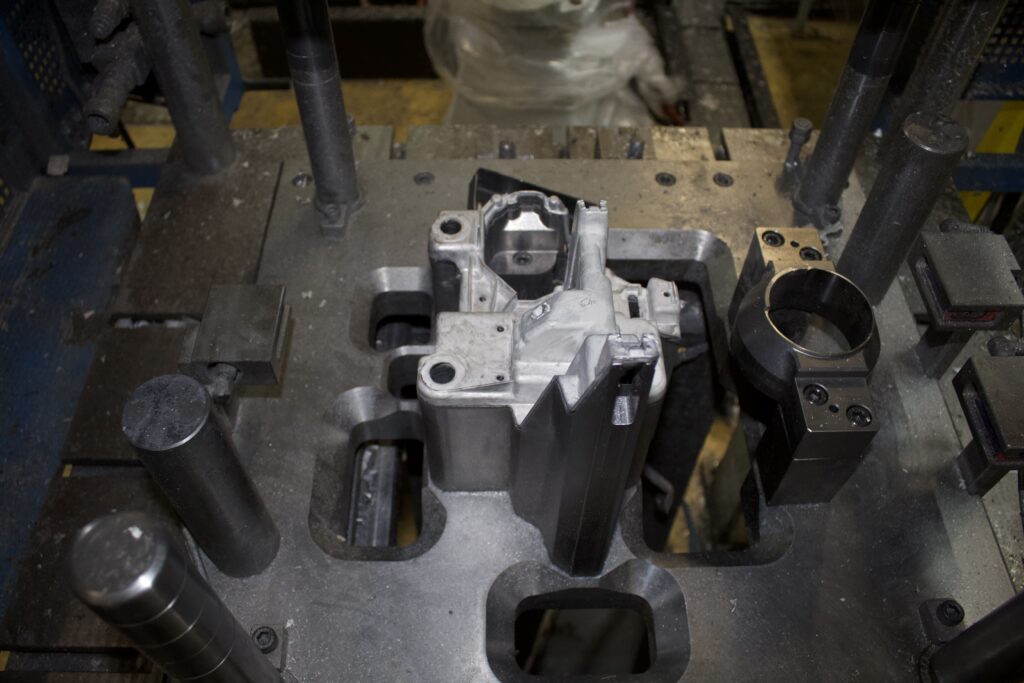
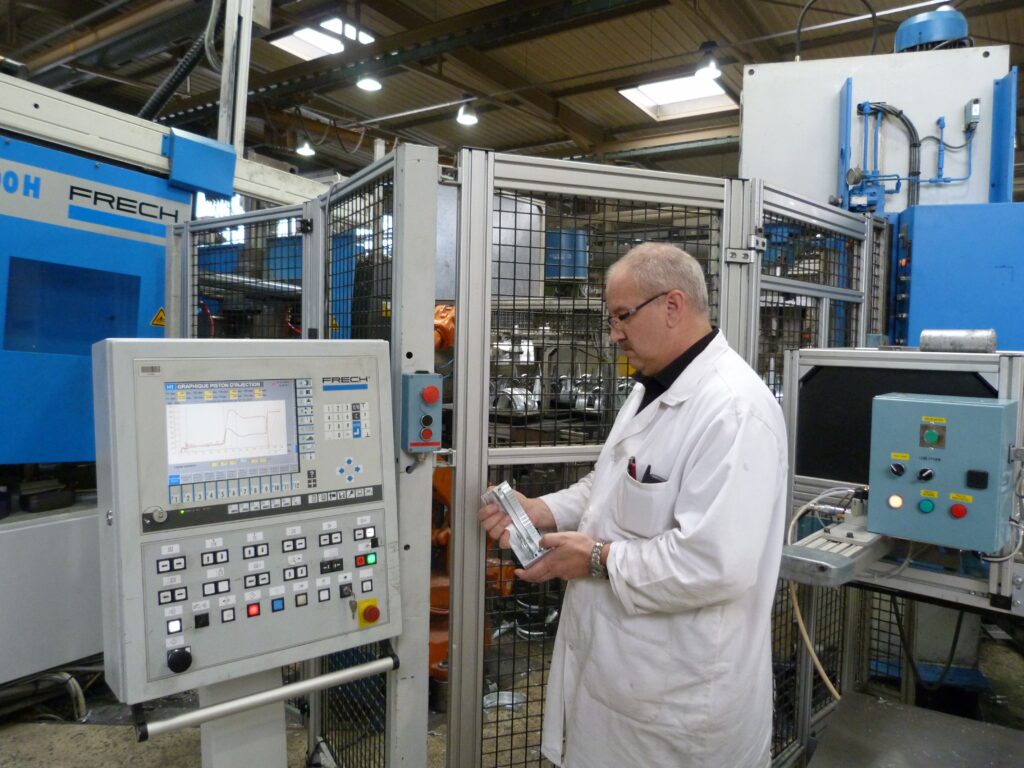
Industrialisation
Thanks to our industrialisation process, supported by state-of-the-art equipment including robotised hot-chamber die casting machines, we process 3,000 tonnes of alloys a year, producing more than 35 million parts. Our parts are characterised by their highly technical nature, complex shapes, thinness and multiple finishes.
Calling on ID Casting is the guarantee to have
know-how and interpersonal skills at your side.