ID Casting, our production stages.
Foundry
Zamak foundry
Magnesium foundry
Trimming / Cutting
After injection, the parts need to be separated from the sprue and feeder heads, either by manual or automatic trimming operations, in s tumbler, or using cutting tools for larger, more complex parts.
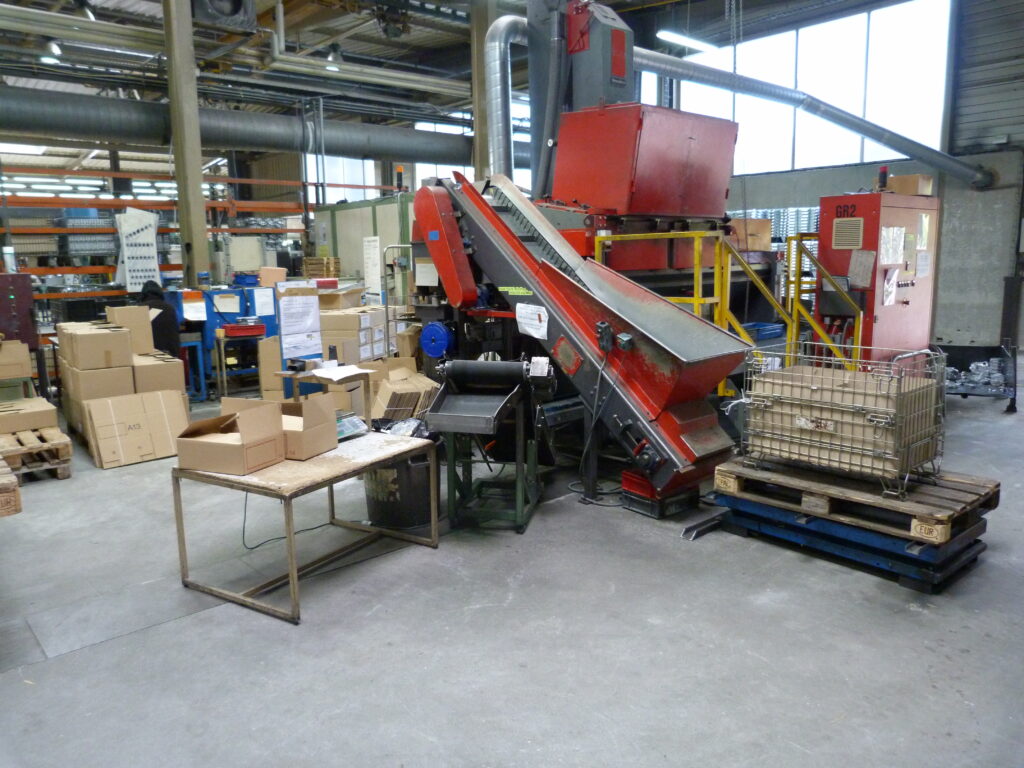
Deburring
and finishing
We tailor our deburring and finishing processes for Zamak and Magnesium parts according to their characteristics and the needs defined by our customers.
Either in-house or with our specialist partners, we use all the technologies to achieve this, enabling us to offer our customers a wide range of solutions such as tribofinishing, tumbling, shot blasting, polishing, bead blasting, thermal deburring, cryogenics, etc. ID Casting’s DNA lies in the quality of the finished product, thanks to high-performance equipment that enables us to check every single part.
Machining
Our machining equipment ranges from traditional, multi-spindle and transfer machines to modern CNC machining centres, enabling us to meet our customers’ machining needs for zamak and magnesium castings in small, medium and large production runs. Machining can be supplemented by additional deburring, washing, impregnation and leak testing, which we carry out in-house or with our specialist partners.
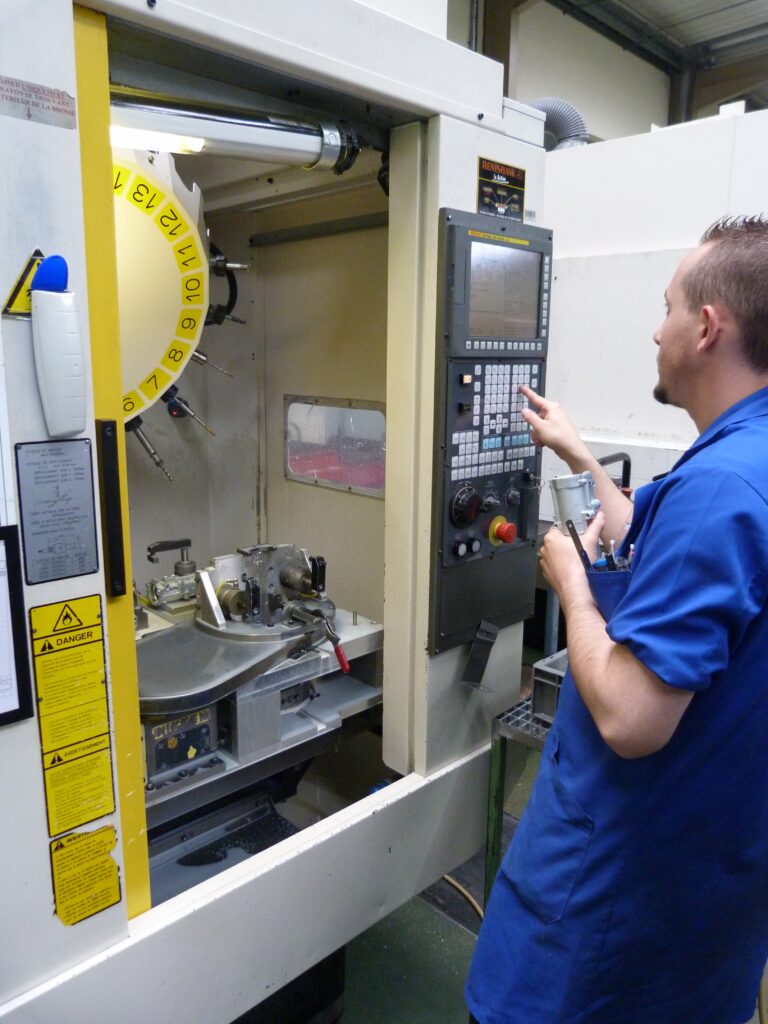

Assembly
Committed to satisfying our customers and providing them with attention to detail, ID Casting offers complementary services: we provide complete assembly, kiting, gluing, inspection and crimping solutions for small, medium and large production runs. Our development and industrialisation teams use the latest technologies on the market to assemble, screw, glue and check with precision, reliability and repairability. Whether using manual, automated or robotic methods, with human or electronic controls, we ensure that each component is assembled and checked according to the defined and expected specifications. At ID Casting, we have the expertise required to carry out complex assemblies, and we are committed to delivering reliable, long-lasting results.
Finishes
We attach great importance to the finish of each part, so we use advanced finishing techniques to achieve aesthetic quality and a smooth surface. We ensure that every part is meticulously finished to the required specification. We are committed to delivering exceptional finished results that meet your highest expectations.
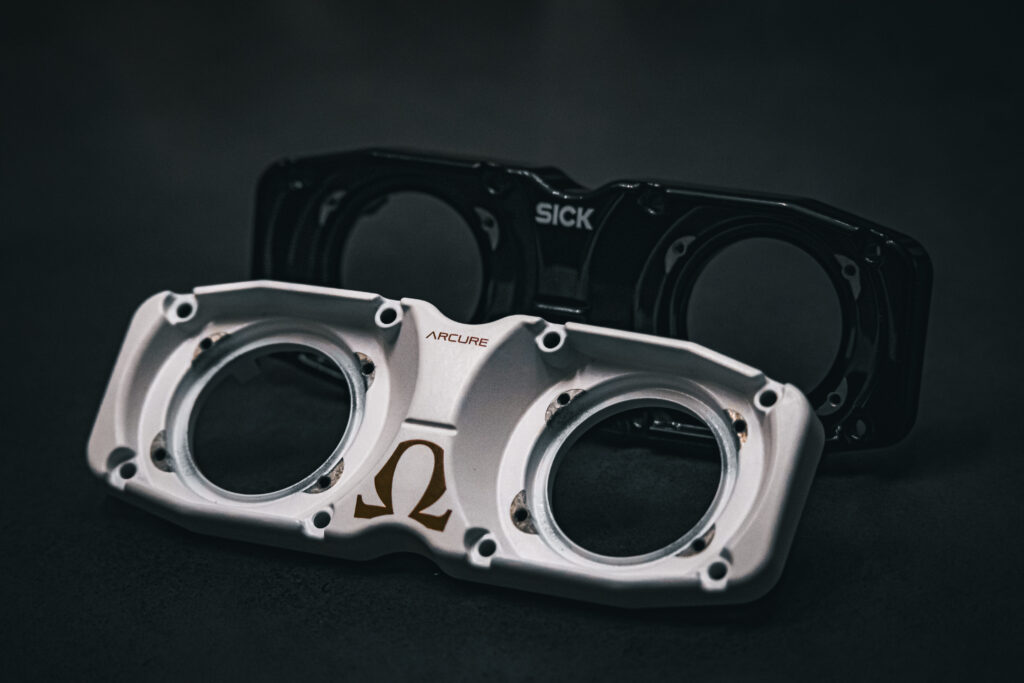
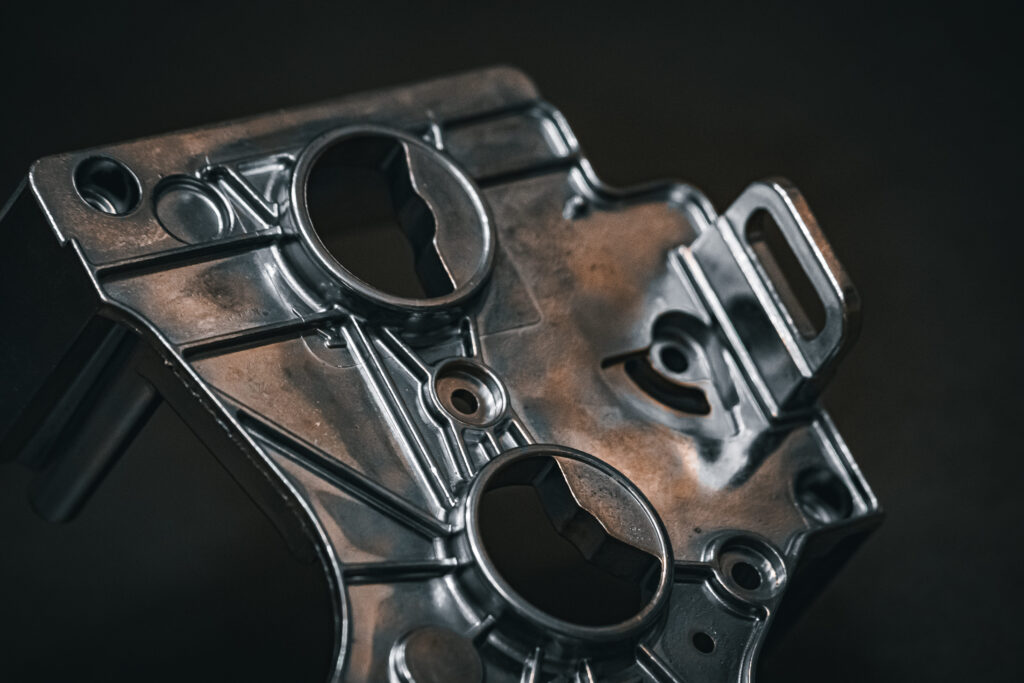
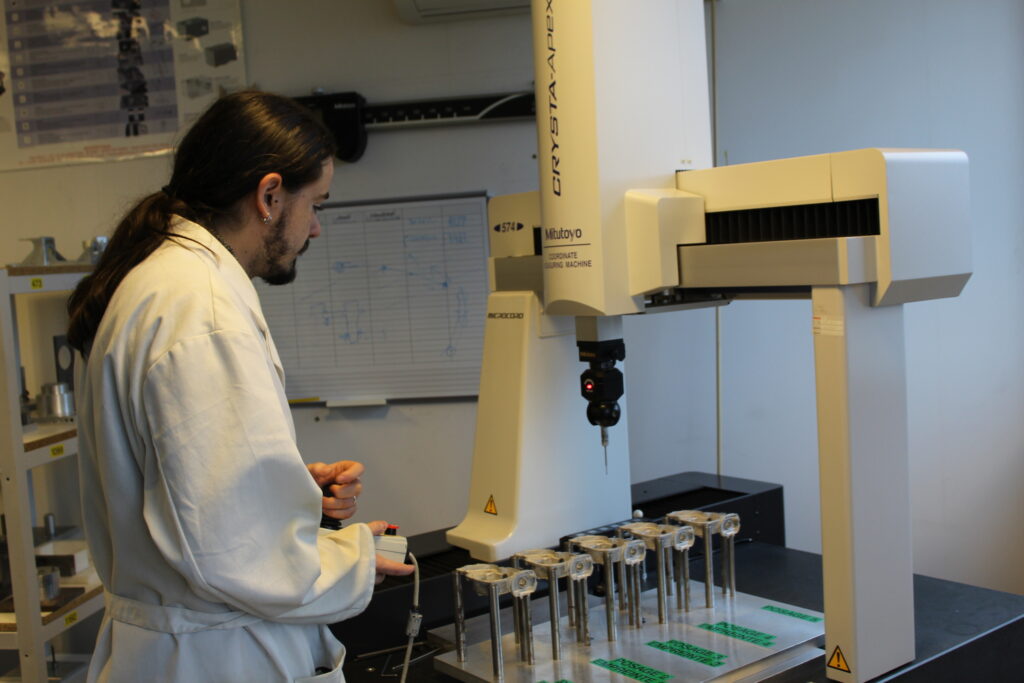
Control
At ID Casting, we pay particular attention to inspection to ensure that our parts are flawless, enabling us to aim for “0” defects.
Our team uses FMEAs to identify the dimensions and criteria to be checked during the production life of products. Then, on the ground, at every stage of the manufacturing process, our quality teams and operators carry out sample checks or 100% checks using advanced control techniques and equipment. This enables us to meet our customers’ most stringent standards, requirements and special characteristics.
Our commitment to quality is reflected in our meticulous approach to detecting defects and imperfections, ensuring first-class results.
Logistics
Logistics is an essential aspect of ID Casting. We are committed to efficient management and on-time delivery of your parts.
We tailor our services to our customers’ needs, and are able to process forecasts and receive orders via EDI or Web-EDI.
Our ERP systems (Capawin and Sylob) combined with our Cyclade production monitoring system enable us to plan, analyse and monitor our production and stocks in real time, with the aim of guaranteeing our customers a service rate of over 96%.
At ID Casting, we strive to provide you with a hassle-free experience when it comes to logistics and delivery, ensuring that your parts reach you on time and in perfect condition.
Our priority? Your satisfaction. We do everything we can to live up to your expectations.
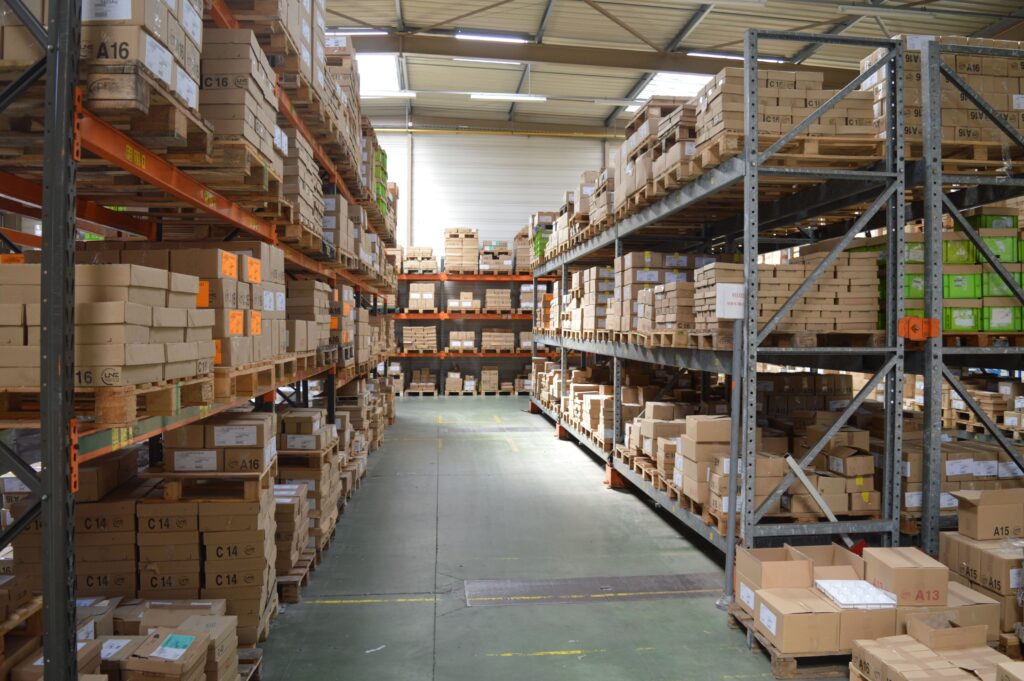
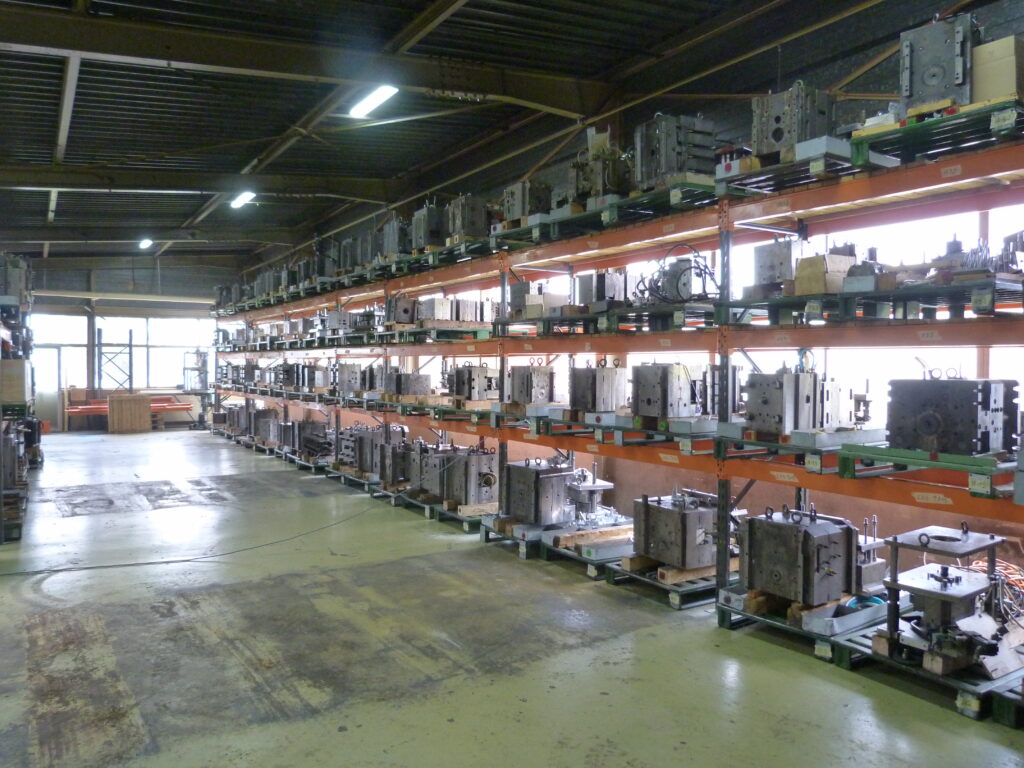
Calling on ID Casting is the guarantee to have
know-how and interpersonal skills at your side.