ID Casting, a sustainable development ethic
Respect for people and the environment are key priorities for the ID Casting group.
Our aim is to reduce our CO2 emissions by 50% by 2025.
A meaningful commitment
to the environment
To offer our customers technical solutions based on zinc and magnesium alloys with characteristics that limit their impact on the environment : recyclability without loss of mechanical properties, fluidity that optimises shapes and mass, limiting energy consumption and finishing operations. Whether it’s product eco-design, staff training or reducing environmental impact, the Group is committed to an environmental charter. With the eco-design requirements of today’s global industries, diecasting remains a model of sustainable development, thanks to its low energy consumption.
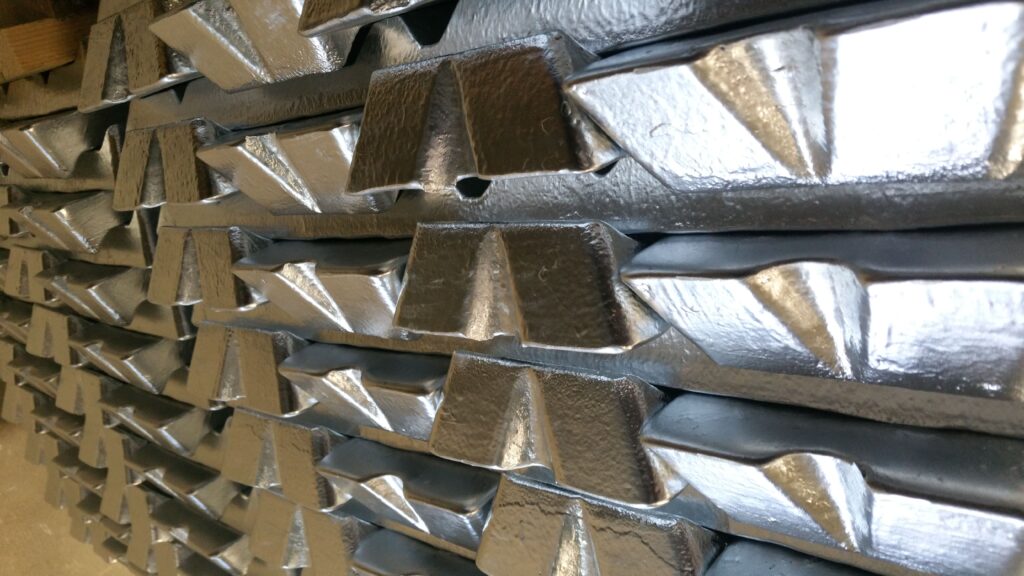
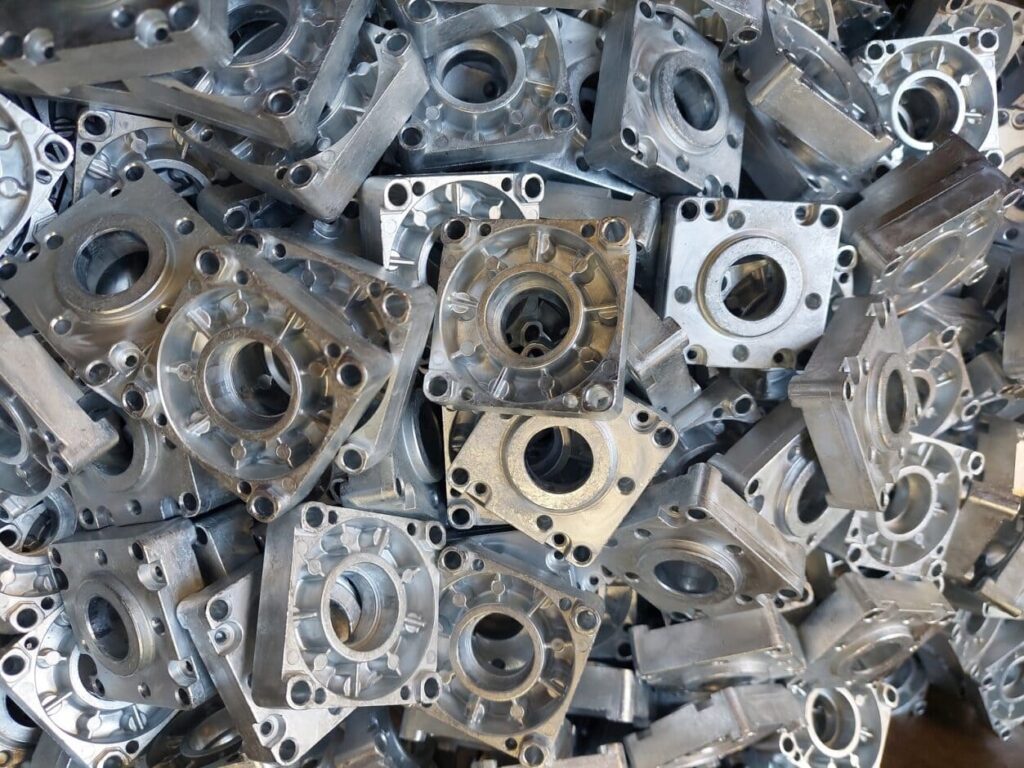
A policy
In constant improvement
ID Casting is committed to respecting the environment in a sustainable way, and is a member of a number of environment-related associations, including ECOVADIS, a specialised CSR platform that enables us to assess our CSR performance as a supplier in order to understand and improve our social and environmental practices.
The EcoVadis rating looks at a broad spectrum of non-financial management systems, in particular their impact on the following themes: Environment, Social & Human Rights, Ethics and Responsible Purchasing. Each company is assessed on key issues according to its size, location and sector of activity.
As an ambassador for innovation, always on the lookout for creative solutions that are consistent with the environment, ID Casting is a member of Expérience Zamak and the IMA (International Magnesium Association). These associations bring together foundries, alloy producers and recyclers, machine manufacturers and industrial equipment suppliers, and users, with the aim of promoting zinc and magnesium alloys.
The global standard for CSR assessments

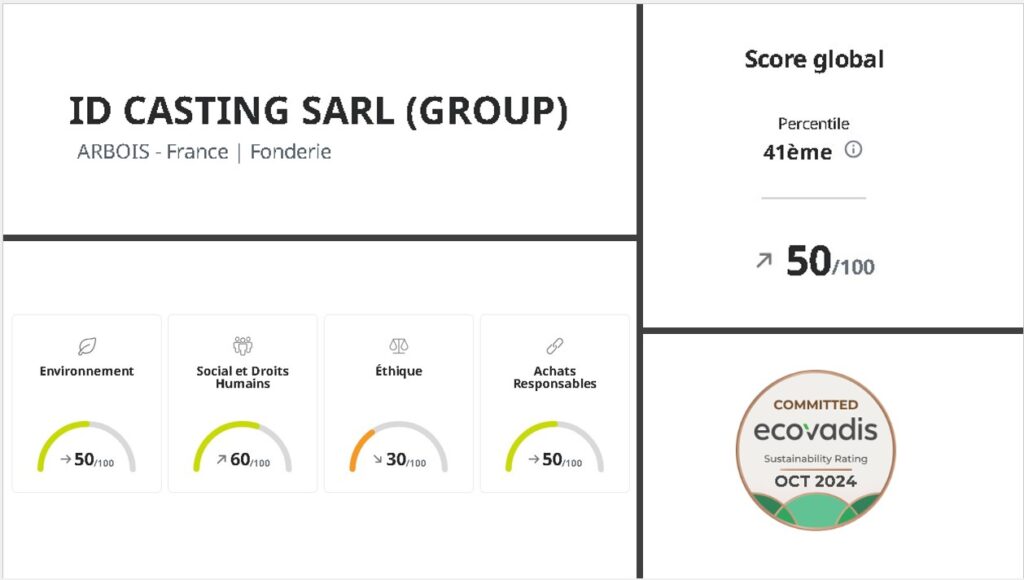
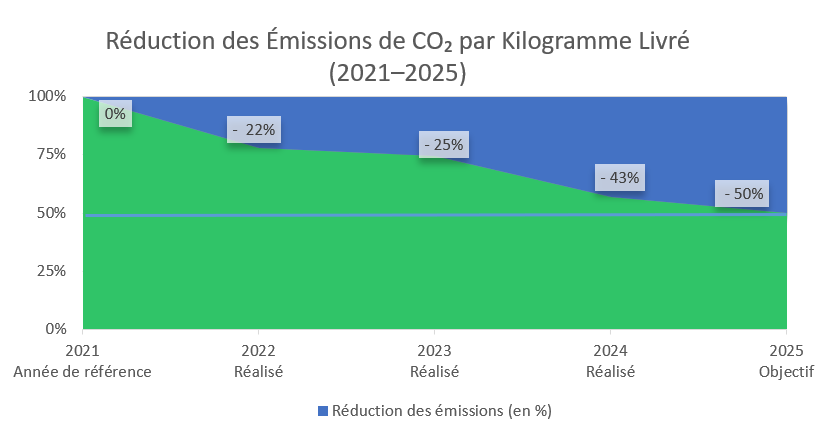
Reduce our CO2 emissions
To address environmental challenges, ID CASTING has implemented an energy-saving plan.
The group first worked on natural gas consumption (building heating) by installing a system that recovers heat dissipated by air compressors and by lowering the setpoint temperature to 19°C in the premises. We are now continuing to optimize the electrical efficiency of processes (compressor modularity based on usage; air network maintenance; furnace insulation; switch to LED technology; process cooling system; adjustment of operating hours according to production load; purchase of renewable energy).
These efforts have been rewarded with a 43% reduction in our CO2 emissions per kilogram of metal delivered in 2024 (54% reduction relative to turnover). ID CASTING aims to reduce its carbon impact by 50% by 2025.
Summary of our CO2 emissions | 2021 | 2024 |
---|---|---|
Scope 1 – natural gas (in tons of CO2 equivalent) | 302.6 | 93.6 |
Scope 2 – electricity (in tons of CO2 equivalent) | 1034.9 | 538.0 |